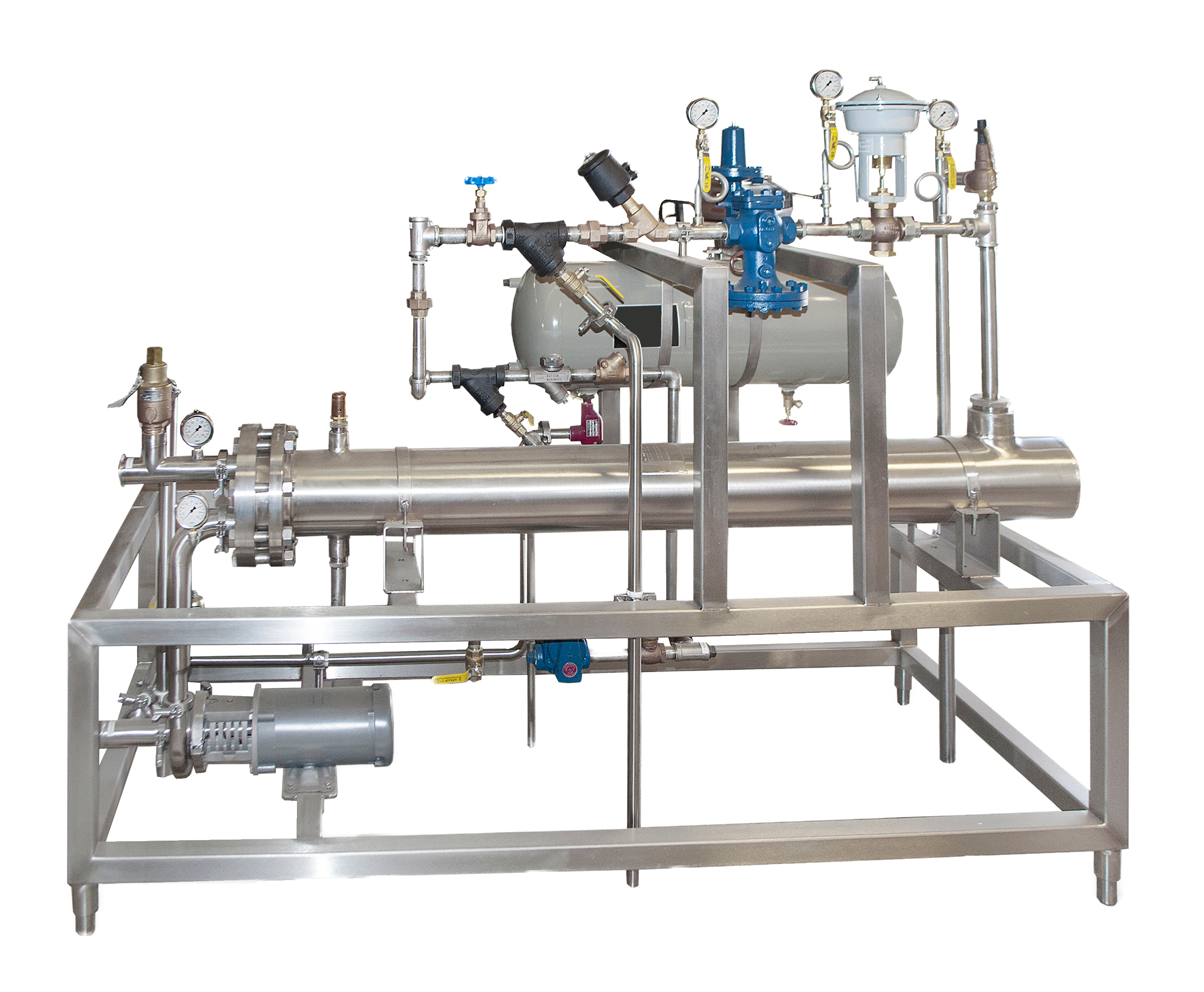
INTRO TO HOT WATER SETS
In this document we will explore every facet involving hot water sets (HWS) so you can be more knowledgeable about the product that you have or are considering buying. We will first discuss the components in which the HWS utilizes, and why each are extremely important. Then we will cover the inner workings of the steam train and explain the process. There are various styles of hot water sets and applications in which they are used throughout the world in different industries which we do our best to pinpoint for you. Finally, we discuss the maintenance that is required, depending on which application and process that will be used.
On a basic level, hot water sets are typically used to generate hot water that will be utilized in other processes. A boiler is used in conjunction to generate steam which is condensed in the hot water set to heat water or other fluid products. Hot water sets are used in a variety of applications ranging from heating small tanks of water or producing large volumes of hot water to be used in commercial food production. At Thermaline, we apply over 30 years of engineering and fabrication experience to create reliable, high quality hot water sets that meet a wide range of process requirements and exceed customer expectations.
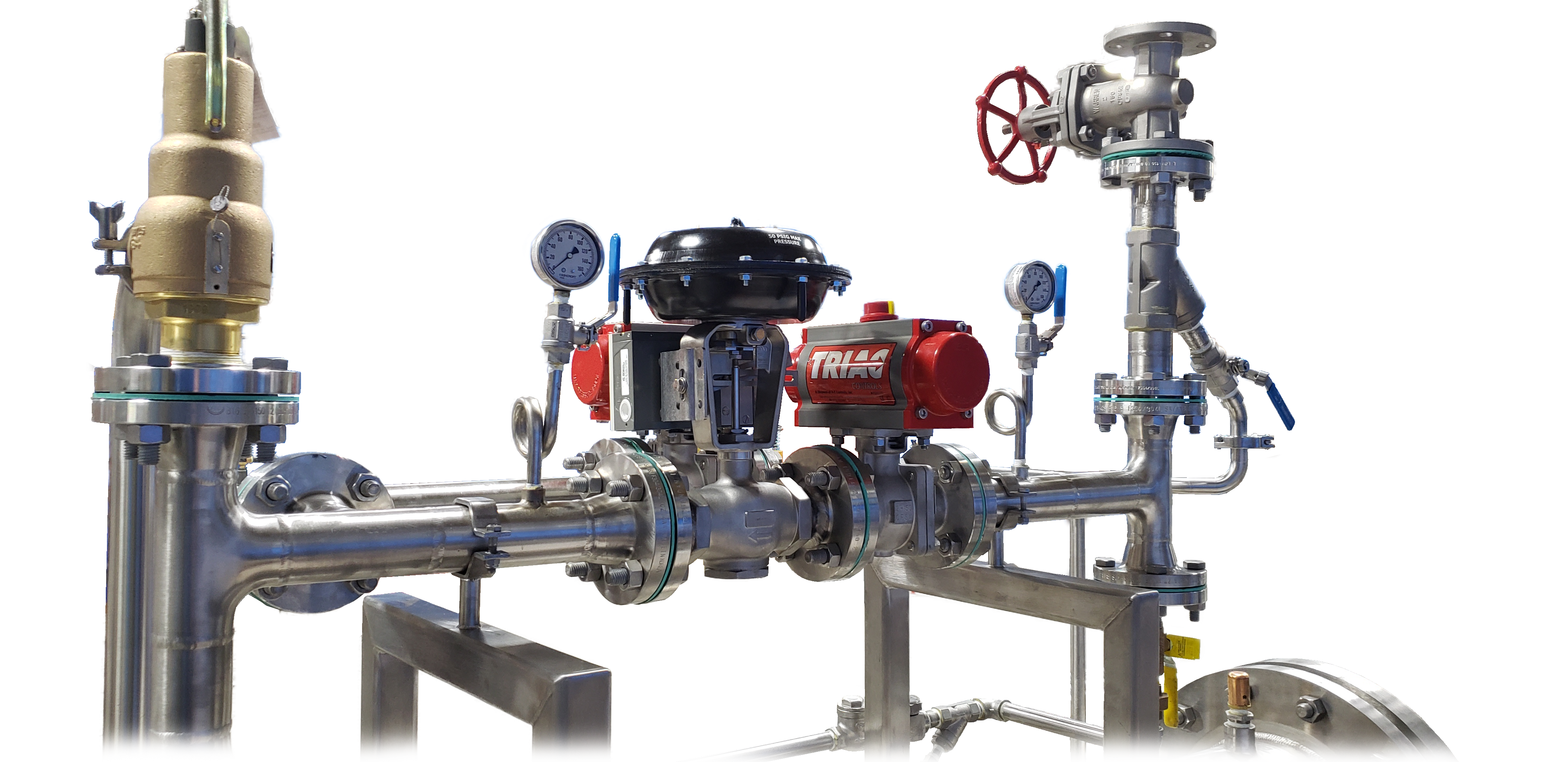
WHAT'RE THEY COMPOSED OF?
Each and every hot water set consists of a steam train and a heat exchanger. The heat exchanger in a hot water set will be either a Thermaline built shell & tube or plate heat exchanger. A shell & tube heat exchanger offers the ability to utilize high pressure steam. Shell & tube heat exchangers have remarkable reliability and are low maintenance but are often more expensive and have a larger footprint than plate heat exchangers. A plate heat exchanger can be used in a low pressure (Less than 50psig steam) steam system. Plate heat exchangers are known for their high heat transfer rates, small footprint and low costs. The benefits of a plate heat exchanger come with the cost of occasional maintenance of the unit which can require gasket replacement. Gaskets used in a plate heat exchanger have a lower life cycle than the stainless steel tube bundle found in the shell & tube heat exchanger (we will go more in-depth about this subject later). The heat exchanger is supplied with steam via the steam train installed in a hot water set.
The steam train of a hot water set is a run of pipe that consists of multiple instruments used to control or direct steam and condensate. The instruments that make up the steam train will vary based on the process and customer needs. Pressure reducing valves (PRV) and control valves are used to control steam pressure or steam flow once the steam has entered the system. Meanwhile, other instruments can be used for equipment safety, display system performance, and ease of maintenance.
Typical equipment on the steam side may include:
- Condensate Pumps (electric or steam pressure motive)
- Pressure gauges
- Safety relief valves
- Isolation valves
- Condensate drip leg
- Y-Strainers
- Bypass lines
- Automatic emergency shut off valves
- Any other specialized components required to meet the process demand.
Typical equipment on the water side may include:
- Hot water pumps
- Thermal expansion tank (compression style or bladder style)
- Water filters
- Backflow preventers
- Water makeup lines
- Air separators
- Safety relief valves
- Temperature gauges
- Pressure gauges
The water side of the hot water set commonly has less components than the steam side. A standard hot water set could be equipped with a hot water pump or expansion tank for a closed loop system. Additional equipment can be added for automatic controls or system displays.
HOW DO THEY WORK?
A hot water set uses steam from a boiler to create hot water in the heat exchanger. The heat exchanger will condense steam to heat the process water. The steam will enter the hot water set through the steam train. A standard steam train will contain valves to modulate and control the steam. A steam pressure reducing valve is often used for high pressure steam systems. By reducing the steam pressure at the hot water set, we can eliminate fluctuations in steam pressure from the supplying steam system. Fluctuations in steam supply pressure are common in high pressure boilers used by large facilities that have multiple processes consuming steam simultaneously. The steam supply is modulated or controlled by the steam control valve. Steam control valves have a range of operation based on the system requirements. Common control valves range from On/off, multi-position, modulating and modulating with electric positioner. All types of steam control valves will work but will have varying amounts of precision. The precision in steam control will change based on the process. Heating a large tank of water over a long period of time will require very little control and a simple on/off valve could suffice. Supplying 168°F water to a dairy pasteurizer will require a higher level of precision to constantly deliver the desired water temperature and will use a modulating control valve with an electric positioner. Once the steam passes through the steam control valve, it will condense in the Thermaline heat exchanger before leaving the system via the condensate trap. The heat exchanger is sized based on water flow rates, steam pressure and the required water temperature rise. All hot water sets will include additional valves and instrumentation. These additional components are used to increase efficiency, ease of maintenance and display system diagnostics. Thermaline will size and select the appropriate instruments to meet your process and allow simple integration of a HWS into a new or existing process systems.
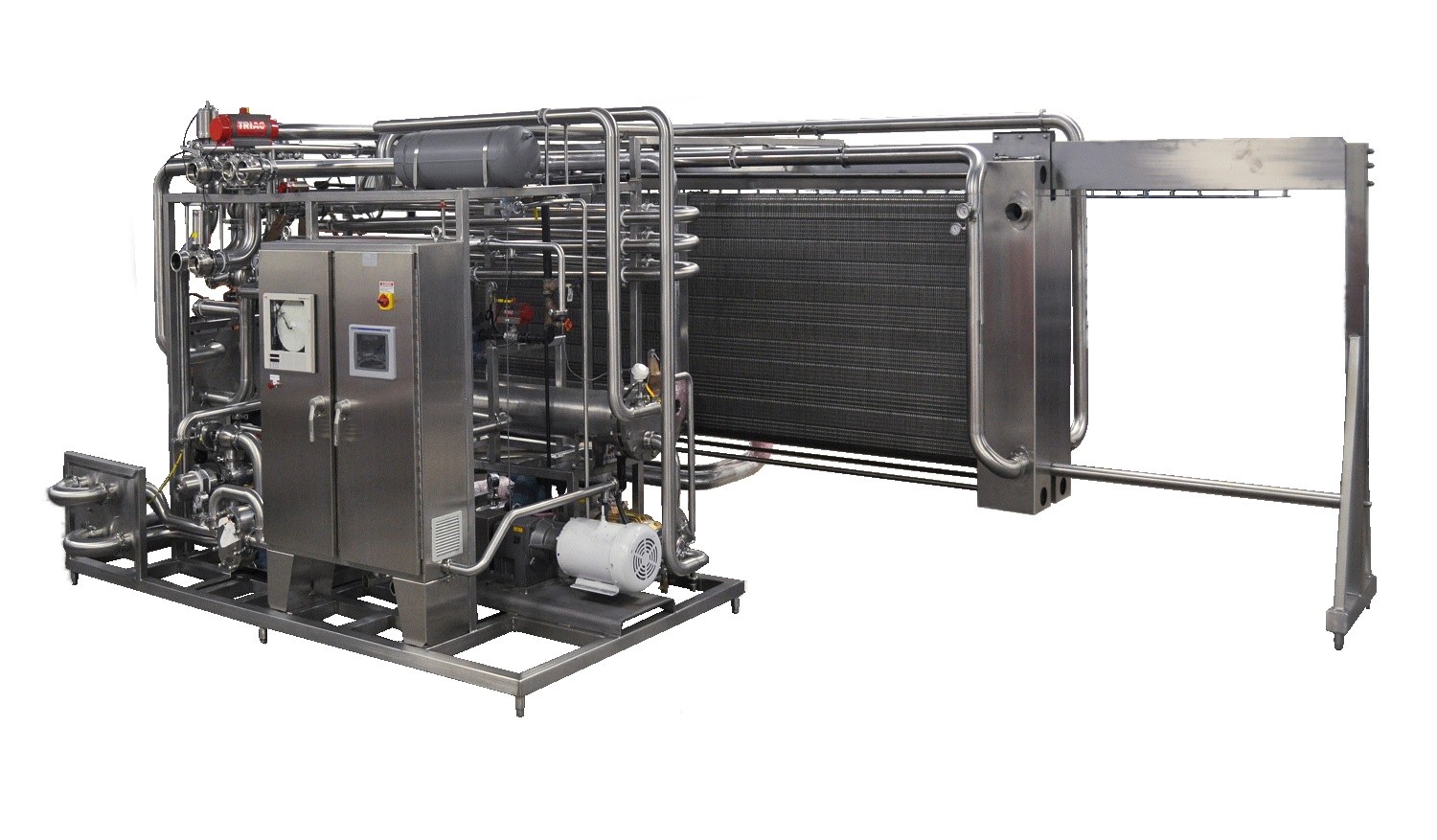
TYPES OF H.W.S.
Hot water systems come as either closed-loop or continuous-loop. The process application will determine what type of hot water set is appropriate.
In a closed-loop system, the water is recirculated through a facility’s system, then back to the hot water set. Closed-loop systems heat and recirculate the same water internally in a closed circuit. Most often this hot water is used for indirect heating in another heat exchanger or a tank jacket. Thermaline’s closed-loop hot water sets will come with a water thermal expansion tank to displace expanding fluids. Additional equipment may be included depending on process requirements.
A continuous-loop hot water set will rapidly heat water that is supplied to and ultimately consumed in another process. The water in a continuous-system passes through the heat exchanger once and is not recirculated through. This water is used in creating a final product. A typical application for a continuous hot water set is batch heating or Clean-In-Place (CIP) processes.
Industries and Applications
Common Industries that Thermaline serves:
- Breweries, cideries, wineries and distilleries
- Food processing
- Beverage processing
- Dairy
- Liquid egg
- Biopharmaceutical
- Oil, gas, pulp/paper, and chemical processing
Common applications for Thermaline hot water sets:
Continuous-Loop System
- Utility water
- Clean-In-Place
- Hose stations
- Instant hot water
Closed-Loop System
- HTST/UNT loop water supply
- Jacketed tanks
Hot Water Set Maintenance
Just like any other machinery, a maintenance plan is crucial to the longevity of your hot water set. Whether it be a daily, weekly or monthly routine, a proper checklist should be put in place. From visibly inspecting the machinery for any leaks to checking gauges to ensure they read correctly. When it comes to the heat exchanger, the gaskets and O-rings need to be periodically checked and eventually replaced (replacement time is dependent on your process and how often your HWS is being used).
The O-ring material is usually Viton which is strong and resistant to corrosion but over time, the elastomers may become cracked resulting in failure. We can see another rare issue which is inherent to the nature of steam trains and failing welds or inner tubes cracking on shell and tube heat exchangers. If this problem ever occurs, a major repair or replacement is required to carry out your process. There are a few ways to check your shell and tube heat exchanger for any internal leaks. Some facilities like to measure the flow of the process fluids to see if any discrepancies are found. Special tools can accurately measure the flow and further pinpoint the epicenter of the issue and ultimately avoid further downtime. This can be done while the heat exchanger is still in use and under pressure. The most popular method is pressure testing. This requires the HWS to be shut off and full access to the HX’s ports. By pressurizing one section of the heat exchanger and adding water to the other section, you will easily be able to detect a leak if there’s bubbling or a loss of pressure. Check out Thermaline’s in-depth discussion about heat exchanger service and repair for more information.
Conclusion
The use of Hot Water Sets is integral to the process of numerous industries. If a large amount of water needs to be heated, chances are a hot water set is used in order to do that. We have the knowledge and experience to accurately customize the best hot water set for your process. Here at Thermaline, we constantly improve our engineering and manufacturing processes to meet today's demands, keep lead times low, and prices competitive. Our online tools allow customers the power to design, receive a quote or purchase in stock equipment instantly and hassle free.
For the last 30 plus years, we have never wavered in our drive for improvement, honing our craft and gathering invaluable industry knowledge. We are experts in heat exchangers and work with the production plants of the nation's biggest brands for food processing, dairy, beverage, breweries, distilleries, cannabis and bio/pharma. Thermaline is the industry standard in heat exchanger engineering, and are certified by BPE, 3-A and ASME. We build all our products to meet stringent consumer safety standards and energy consciousness. Thermaline is a relatively small, nimble team, which allows us to tailor every product to the project you’re working on.